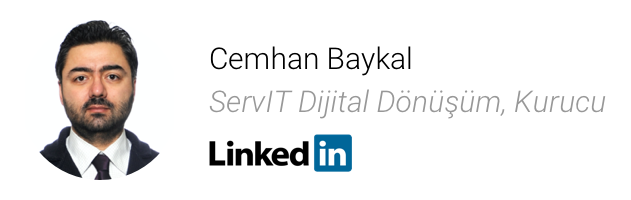
Kestirimci Bakım ve Makinalar
Bir hastalığı tedavi eden belki en yetenekli kişi olabilir, ancak bunu önleyen en güvenilir doktordur.
Thomas FULLER
Endüstri 4.0 kapsamında Kestirimci Bakım, işlem ve makine verilerinin değerlendirilmesine dayanan bir bakım sürecini ifade eder. Temel verilerin gerçek zamanlı işlenmesi, ihtiyaç temelli bakımın temelini oluşturan tahminlerin yapılmasını ve sonuç olarak kesinti sürelerinin azaltılmasını mümkün kılar. Burada sensör verilerinin doğrudan cihazlardan alınması, iletilmesi ve bir karar destek sistemine ulaştırılarak;
- İnsan analizi
- Önceden tanımlanmış algoritmalar/ statik politikalar(policy)
- Yapay zekâ tabanlı sistemler
Aracılığıyla yorumlanmaları gerekmektedir. Bütün bu işlemler sonucunda bir sorunu ortaya çıkmadan çözmek için bir bakım teknisyeni atanabilir. Çünkü, iş hedeflerine ancak tesisler, makineler ve süreçler mükemmel bir şekilde çalışırsa ulaşılabilir.
Kestirimci Bakım Teknolojileri yardımıyla, bakımın ne zaman yapılması gerektiğini tahmin etmek için makinelerin durumu değerlendirilir. Kestirimci bakımın temel amacı, en hassas ileri bakım planlamasını sağlamak ve beklenmedik arızalardan kaçınmaktır. Belirli bir makineye ne zaman bakım yapılması gerektiğini bilmek, yedek parça veya personel gibi bakım işleri için kaynak planlamayı kolaylaştırır. Ayrıca, “planlanmamış duraklar” daha kısa ve daha sık “planlı duraklara” dönüştürülerek sistem kullanılabilirliği artırılabilir. Diğer avantajlar arasında, tesislerin potansiyel olarak daha uzun hizmet ömrü, artan tesis güvenliği, çevre üzerinde olumsuz etkileri olan daha az kaza ve optimize edilmiş yedek parça kullanımı bulunmaktadır.
2018 yılında Almanya’da yapılan bir araştırmaya göre kestirimci bakım ile aşağıdaki kazanımlar sağlanmıştır:
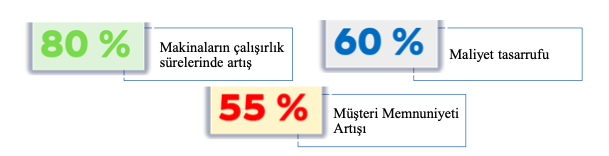
Kestirimci Bakım Nasıl Çalışır?
Kestirimci bakım, fabrikaların/üretim atölyelerinin durumunu periyodik (çevrimdışı) veya sürekli (çevrimiçi) kontrol ederek kategorilere ayırır. İdeal durumda, yaklaşan bakımı sadece mümkün olduğunca düşük maliyetli değil, aynı zamanda performans açısından verimli, yani makine performans kaybetmeden önce yapmak mümkündür. Düzenli sistem işletimindeki kesintileri minimumda tutmak için, en öngörülü denetimler tesis işletimi sırasında yapılabilir.
Bir makinenin gerçek durumunun değerlendirilmesi için kızılötesi, akustik (kısmi deşarj ve ultrason), titreşim analizi ve ses seviyesi ölçümleri ile bir inceleme kullanılabilir. Elbette, bu test prosedürleri makinenin işlevini bozmamalı ve hatta ona zarar vermemelidir. Daha yeni bir yaklaşım, bundan elde edilen bilgileri, işbirlikçi süreç otomasyon sistemleri tarafından sağlanan süreç performans verileriyle ilişkilendirmektir. Firmanızda öngörülü bakımı etkili ve uzun vadede uygulamak istiyorsanız, aşağıdaki üç adımı izlemelisiniz:
- Verilerin yakalanması, dijitalleştirilmesi ve iletilmesi,
- Toplanan verilerin depolanması, analizi ve değerlendirilmesi
- Belirli olayların meydana gelme olasılıklarının hesaplanması.
Ben, Firmam ve Kestirimci Bakım
Dijital Dönüşüm yolculuğunuzda, makineleriniz için kestirimci bakıma dönüşmek zor görünebilir çünkü küçük performans değişikliklerinin uygun araçlar olmadan tespit edilmesi karmaşık bir süreçtir. Durum izleme, kestirimci bakımda önemli bir rol oynar ve maliyetli arıza sürelerinin önlenmesine yardımcı olur. İzlenmesi gereken önemli bir koşul titreşimdir. Makine titreşimi genellikle dengesiz, yanlış hizalanmış, gevşek veya aşınmış parçalardan kaynaklanır. Titreşim arttıkça, makineye zarar verebilir. Titreşimdeki artışlar için motorları, pompaları, kompresörleri, fanları, üfleyicileri ve dişli kutularını izleyerek, sorunlar şiddetlenmeden önce tespit edilebilir ve planlanmayan arıza süresine neden olabilir.
Ancak bu o kadar da zor değil…
Öncelikle makinaların üzerine konumlandırılabilecek sensörlerin birkaçından bahsedelim:
- Titreşim Sensörleri
- Yağ partikül Sensörleri
- Tork ölçüm Sensörleri
- Akım Sensörleri
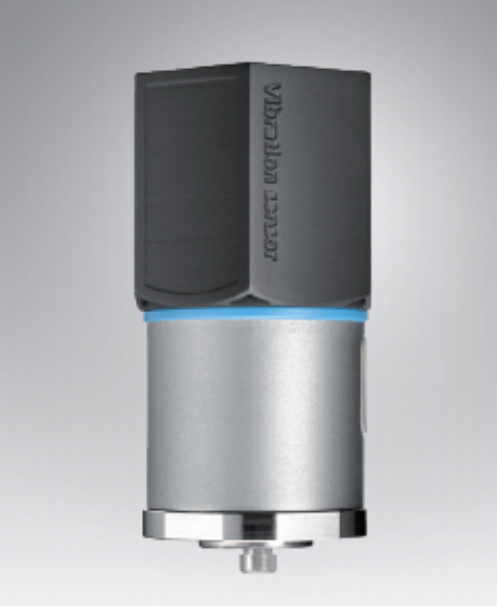
Titreşim sensörleri, makinaların üzerine konumlandırılarak aşağıdaki değerleri ölçen ve dışarıya çeşitli sinyal protokolleri ile bilgi olarak aktaran cihazlardır:
- Hız (Ortalama Karekökü)
- İvme (Ortamala Karekökü ve Zirve değeri)
- Deplasman (yer değiştirme)
- Basıklık (Kurtosis)
- Tepe Değerlerin Etkin değerlere Oranı (Crest Factor)
- Çarpıklık (Skewness)
- Standart Sapma
Yağ partikül sensörleri ise genellikle dişli ve aktarma elemanlarının bulunduğu vites kutusu gibi alanlardaki yıpranmayı ölçmektedirler. Temel çalışma prensipleri, kapalı bir hacimdeki aşınma/yıpranma partiküllerinin miktarını ölçmek ve demir/demir olmayan şeklinde nitelendirmektir. Genellikle motorların yağlama ünitelerine entegre edilerek çalışırlar.
Tork ölçüm sensörleri ile motor, krank mili, şanzıman, rotor gibi dönen bir sistemdeki torku ölçmek ve kaydetmek mümkün olabilmektedir. Statik torkun ölçülmesi dinamik torkun ölçülmesine göre kolaydır. Dinamik torkun ölçülmesindeki zorluk genellikle ölçülen şafttan bir miktar etkinin (elektrik, hidrolik veya manyetik) statik bir sisteme aktarılmasını gerektirmesidir. Bunu başarmanın bir yolu da şaftı veya şafta tutturulmuş bir parçayı bir dizi kalıcı manyetik alan ile koşullandırmaktır. Bu alanların manyetik özellikleri uygulanan torka göre değişecektir ve bu nedenle temassız sensörler kullanılarak ölçülebilir. Genellikle, tork sensörleri veya tork transdüserleri dönen bir şaft veya aksa uygulanan gerinim ölçerler kullanır.
Son olarak da Akım Sensörlerinden bahsedebiliriz. Aslında akım sensörlerinin ana kullanım amacı enerji yönetimidir. Aslında akım sensörlerinin ana kullanım amacı enerji yönetimidir. Ancak
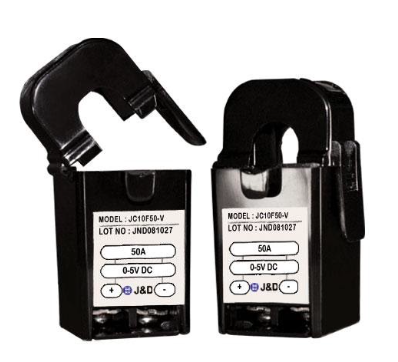
özellikle elektrik motorları veya jeneratör mantığındaki sistemlerde akım aşımlarının ölçülmesi, kestirimci bakım için kullanılan sensör/ölçüm sistemlerinden biri haline getirmiştir.
Akım transdüserleri, dağıtılmış güç hattı taşıyıcıları (PLC’ler) veya otomasyon ve denetim için SCADA yazılımı gibi uzaktan kumandalar sistemindeki akım ölçümü için de uygulanabilir. Diğer uygulamalar arasında güvenlik ve durum izleme, yük izleme, koruma sistemleri ve konveyörlerin, pompaların, HVAC motorların ve daha fazlasının tahmini bakımı yer alır. Yük akımı ile orantılı olarak analog enstrümantasyon sinyalleri veren bir sensör doğrudan dağıtım panosunun ana veya branşman kablolarına kenetlendiğinde, PLC veya veri kaydedici ortada bir dönüştürücü olmadan analog porta doğrudan giriş sağlanır. Ayrıca motorların boşa düşmeleri veya kısa devrelerin fark edilmesinde de iş görürler.
Makinamdan Veriyi Aldıktan Sonrası?
Sensörler hem her şeydir hem de kendi başalrına hiçbir şeydir. Sinir sistemimizdeki sinirler ile sensörler aynı görevi görürler. Esas işi ise sinir iletim demetleri ve sonrasında beyin gerçekleştirir.
Fabrikadaki makinaların üzerine bu sinir uçlarını yerleştirmek için eskiden uzun kablolamalar yapmak, sinyal tekrarlayıcılar, güçlendiriciler koymak zorundaydık. Şimdi ise bu sensörlerden aldığımız veriyi kablosuz olarak çok geniş fabrika kampüslerinde, kapalı alanlarda dahi taşımamız mümkün. Genellikle ModBUS, MQTT veya HTTP iletim gerçekleştirebilen bu cihazlar LP, LORAWAN, WI-FI, LTE/GSM gibi sinyal protokolleri ile de kısa ve uzak mesafeler için çeşitli opsiyonlar ile kullanıma hazır durumdalar. Bu cihazlar çok küçük form faktörler ile üretilmeleri, batarya ve güneş enerjisi beslemeli türlerinin de üretilmiş olmaları ve düşük maliyetleri ile hızlı bir dijital dönüşüm için büyük bir kolaylık sağlamaktalar.
Veriyi sensörlerden toplayıp sinir iletim demetlerimiz olan sinyal aktarıcıları da kurduktan sonra artık bu veriyi anlamlı olarak kullanmak gerekmektedir. Aslında bu noktaya kadar gelecek bir vizyona sahipseniz zaten ne yapmak istediğinizi biliyorsunuzdur. Örneğin kestirimci bakım uygulamalarındaki en klasik yöntem, eşik değerler belirleyip takip edilen sistemin anomalileri durumunda alarmlar üretmek veya sıklıklarına göre hataları, arızaya dönüşmeden fark etmektir. Bir diğer izleme tekniği de belirli bir geçmiş zaman tarihçesindeki trendleri takip edip anomalileri değerlendirmektir. Bu tür politikaları çok çeşitli şekillerde kurabilmeniz için Thingworx gibi platformları kullanabilirsiniz. Ayrıca yine sensör/gateway üreticilerinin sunduğu bulut tabanlı çözümlerle de bazı hazır verilerden faydalanabilirsiniz.
Yapılacak Sistemin Yatırımının Geri Dönüşü (ROI)
2013’te J Christensen, W.H. Graf ve T. Young tarafından bir rafineride yapılan araştırmaya göre:

Aynı ekibin kestirimci bakım çalışmaları ile elde ettiği sonuç çok etkileyici:
Günlük üretimi 100.000 varil olan bir rafineride elde edilen yıllık kazanım, 3,5 M USD. Bunun kırılımı da şöyle:
- Anormal olayları önlemek sonucu kazanım : 500.000 USD
- Kaybedilen kârın fırsat değerinden elde edilen kazanım : 1.750.000 USD
- Bakım bütçesinin azaltılmasından elde edilen kazanım : 800.000 USD
- Ekip üretkenliğinin artışı sonucu elde edilen kazanım :300.000 USD
- Sigorta priminden elde edilen kazanım :200.000 USD
Özetlersek,
- Kestirimci bakım bir yan fayda değildir; doğal ve temel bir süreciniz olarak görmelisiniz. Rutin ya da arızi bakımların aslında sizin üzerinizde yük olduğunu içselleştirin.
- Çok basit kestirimci uygulamalarını çok büyük projeler tasarlamadan başarabilirsiniz.
- Makinalarınız için sensörler ve kablosuz ağ araçları ile işe başlayın. Küçük birimlerinizde hızlı uygulamar ile yol alın.
- Makinalarınızı izleyin-takip edin. Ne zaman sorun yaşamaya meyilli olacaklarını baştan tanımlayın. Belirlediğiniz politikalar ile arızaları önden kestirin. Makinanızın sağlığındaki trendleri takip edin.
- Bütün bunlar için yeni makine yatırımları yapmanız gerekmez; mevcutlara basit eklentiler ile sonuca gidin.
- Bu küçük projeler için yapacağınız yatırımları CFO’nuza anlatırkan elde edebileeğiniz kazanımları yukarıdaki şekilde anlatın. Buradaki kazanımların birçoğu gözle görülmeyen ama varlığını her zaman şirket finanslarınız üzerinde hissettirecek türdekilerdir.