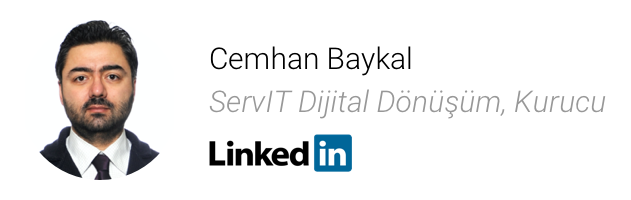
Eğer bir fabrika sahibiyseniz, fabrikanızda üretim yapılan her gün yaptığınız üretimin sabit bir paydaşı olarak enerji maliyetlerinizi hesap etmek durumundasınız. Hammadde alırken, personel ücretlerinizi hesaplarken, döviz kurunu takip ederken bu enerji maliyetleri hep oradadır ve zaten enerjiyi tükettiğiniz için faturası zarfın içerisine konmuş ofisinize doğru yola çıkmıştır bile.
Çok iyi bir maliyet muhasebesi sistemi kursanız bile, ürettiğiniz ürünün bilfiil içerisindeki enerji payını kati rakamlarla hesap etmeniz oldukça güçtür. Dolayısıyla, bir birim ürün içerisindeki enerji tüketimini aslında hesaplamazsınız. Yaptığınız şey daha çok muhasebenizin genel tablolarına bakmak ve zaman içerisinde enerji maliyetlerini önlemler alarak kısmak olacaktır.
Dijital Dönüşüm ise size başka bir yol çizmekte… Enerji maliyetlerinizi düşürmenin esas yolu enerji verimliliğinizi artırmaktan geçer. Bunu yapabilmek için de tüketimi gerçekleştiren her bir bileşenin durumunu bilmeniz ve buna yönelik alternatifler aramanız gerekecektir. Bu noktaya geldiğinizde sizi şu üç temel soru karşılamaktadır:
- Nereden başlamalıyım?
a. Hangi üretim biriminin enerji tüketiminde en fazla verimlilik artışı sağlayabilirim?
- Nasıl yapmalıyım?
a. Üretimde aynı işi yapan ama Verimlilik açısından en büyük yararı sağlayan birimleri nasıl önceliklendirebilirim?
b. Eski cihazları yenileriyle mi değiştirmeliyim? Yatırım ve İşletme maliyetleri açısındanbileşen bazlı bir ROI(Yatırımın Geri Dönüşü) hesaplamasını nasıl yapabilirim?
- Nasıl sürekli kılarım?
a. Bütün bu verimlilik çalışmalarını yapsam bile elde edeceğim faydayı sürekli kılabilmemin yolu nedir?
b. Yapacağım yeni hat/kapasite yatırımları ya da değişikliklerinde verimlilik ile ilgili bütün kurguları nasıl denetim altında tutabilirim?
Endüstri 4.0’dan önce Endüstri 3.0 vardı
1969 yılında ilk PLC’nin üretim hayatına girmesiyle başlayan Üçüncü Endüstri devrimi (Endüstri 3.0) aslında Otomasyon devrimi olarak da tanımlanır. Bilgisayar sistemlerinin otomasyona yön vermesi ve çeşitli elektronik kontrol devrelerinin mekanik sistemleri kontrolü ile başlayan bu dönemde her bir sistemin başlıca üretim metrikleri veri olarak oluşmaktaydı. Ancak şunu özellikle belirtmekte yarar var: “Bu veriler bağlı ve anlamlı değildi!” Yani:
- Bu veriler karşılaştırılabilir değildi.
- Bu verilerden bir analitik üretmeniz için insan etkisine ihtiyaç vardı.
Bu durumda bir fabrikadaki çok sayıda farklı birim için bu verileri makinalar üzerinden toplamanız güçtü. Özellikle de enerji tüketimleri konusunda ya hiç ya da çok kısıtlı bilgiler alabildiğiniz bu ürünler size üretim maliyetleriniz konusunda bir fikir vermiyordu.
Bugün ise durum farklı…
Verileri toplamak hiç bu kadar kolay olmamıştı
Öncelikle size enerji tedarikini yapan firmanın trafosundan kendi uç üretim cihazınıza ya da üretim hattınıza kadar enerji tüketimi verilerini almak ve ilişkilendirmek noktasında imkanlarımız gelişti. Birkaç yoldan bu verileri toplayabiliyoruz:
- Trafolar üzerine Enerji Analizörleri takarak
- Hatlarınız ve cihazlarınız üzerine akım trafolarıyerleştirerek
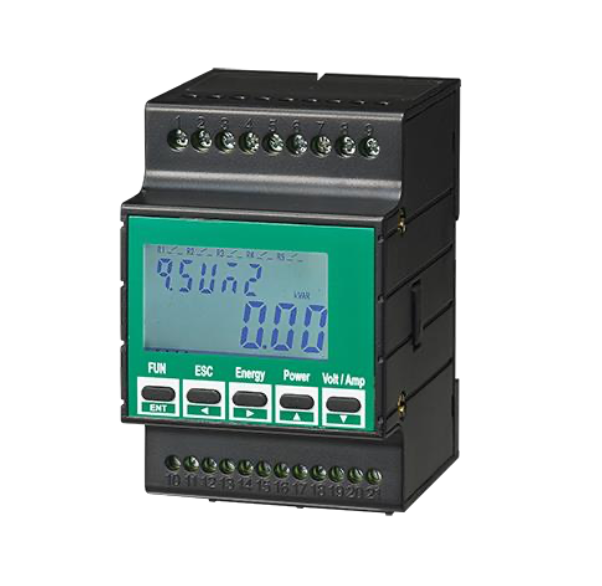
Bu verileri aldıktan sonra fabrika içerisinde kablolama yapmak ile uğraşmanıza da gerek kalmadı. Artık Doğrudan bu analizörleri üzerinden WiFi, LPWAN ya da LoRaWAN gibi kablosuz iletim yöntemlerini kullanmanız mümkün. Enerji analizörlerinin önüne koyacağınız kablosuz alıcılar son derece eknomik ve sizi bu kablolama zahmetlerinden de kurtarmakta.
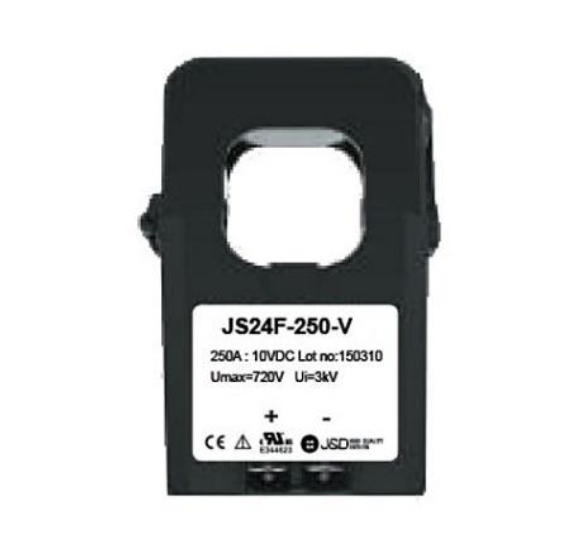
Enerji analizöründen alacağınız ve alçak ya da orta gerilim hatlarınızın enerji değerlerini gösteren veriler size üretim birimleriniz bazında en büyük tüketimin nerede olduğunu gösterecektir. Her bir hattın önüne bağlayacağınız akım trafoları ile de bu tüketim değerlerini orantılayabilir ve geriye dönük olarak da tarihçe oluşturabilirsiniz.
Bütün bunların sonucunda üretim miktarı bazına enerji komponentizasyonunu sağlamanız mümkün olacaktır. Her bir ürünün üretim aşamasına ne kadarlık bir tüketimin dahil olduğunu görebilir ve ürünün her aşaması için bu değerleri değerlendirebilirsiniz. Örnek oalrak yapabileceğiniz en kolay iş, bu hatlardaki motor, pompa, kompresör gibi doğrudan üretim miktarına bağlı olamayan cihazları ölçeklemeniz olacaktır.
Özellikle son 20 yıl içerisinde motorlardaki verimliik konusunda büyük gelişmeler kaydedilebildi. Bu noktada birkaç bilgiyi sunmak istiyorum:
IEC ve TSE tarafından da yayımlanmış Endüstriyel amaçlı satışa sunulan Alçak Gerilim Motorları için Enerji Verimliliği sınıflandırması söz konusu:
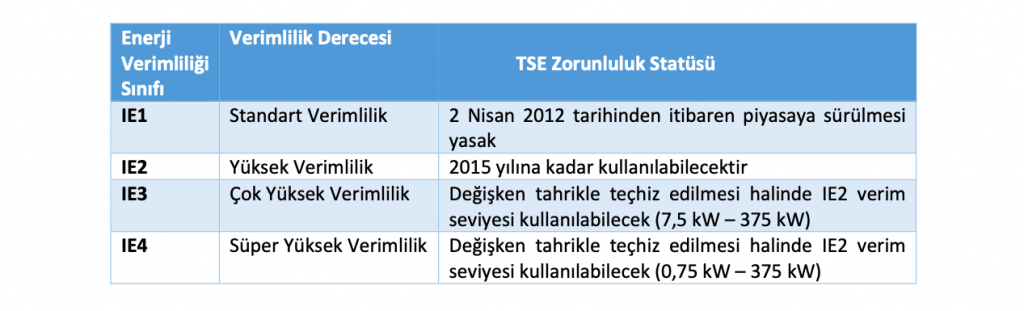
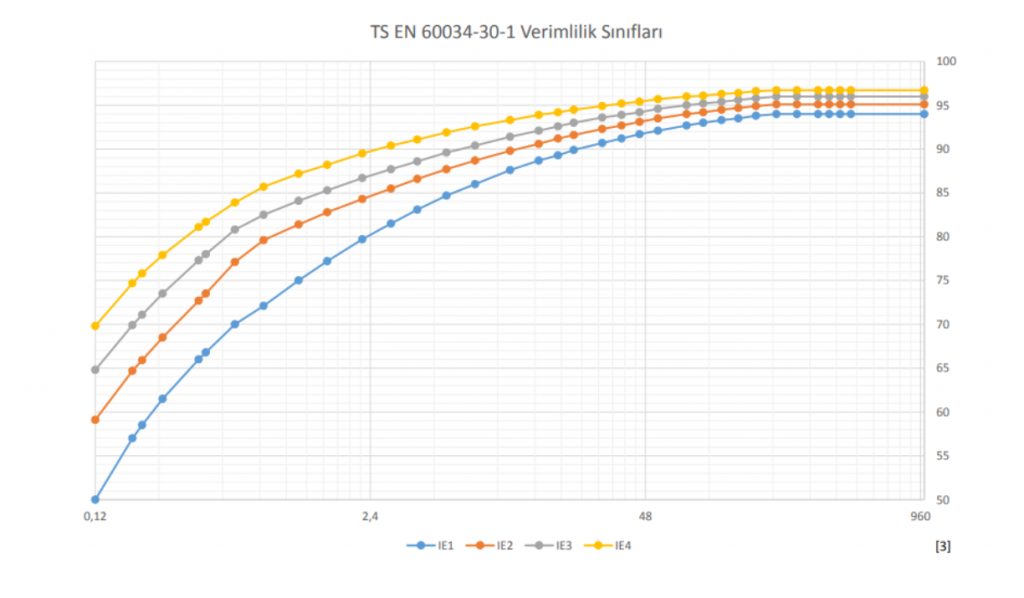
Yukarıdaki verimlilik sınıflandırmalarına referansla bir örnek yapalım:
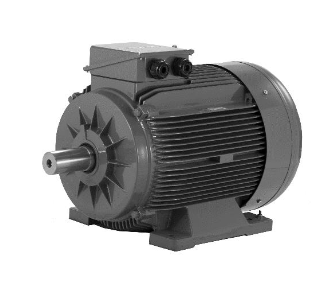
A Fabrikasının elinde 1990’lı yıllarda fabrikanın kuruluşu/yenilemesi sırasında tedarik ettiği 1 adet 4-kutuplu 45 kW’lık IE1 sınıfı motor bulunmaktadır. Bu motorların sürekli çalıştığını varsayalım. Eylül 2020 itibariyle endüstride 1 kWh’lik enerji tüketimi bedelinin 0,49 TL olduğunu söyleyebiliriz. Buna göre, %91,7 verimle çalışan bir IE1 sınıfı motor, 1 saatte 49,0731 kwH harcayacaktır. Bunun yıllık tüketim (8760 saat) karşılığı ise 429,880 kwH’tir. Bu motorun aynı güçte bir yeni IE4 sınıfı motor ile yenilenmesi durumunda ise 1 saatte harcanan güç 47,1698 kwH olacaktır. Bu motorun değiştirilmesi durumunda 8169 TL enerji tüketimi tasarrufu elde edilecektir. Yine 2020 Eylül ayında 45kwH’lik 4 kutuplu bir motorun fiyatının 6500 TL +KDV olduğu görülmektedir.
Buna göre 1 yıldan kısa bir sürede sadece enerji verimliliği ile elde ettiğiniz getiriyle bu tür bir ekipman değişimi yatırımını gerçekleştirebiliyorsunuz. Bunun üzerindeki her yıl için de yine bu tasarrufu finansal gider tablonuza işleyebiliyorsunuz.
Bütün bunları yapabilmek için öncelikle mevcut tüketimlerinizi ve tüketim zaaflarınızın öncelikli olduğu uç birimleri tespit edebilmeniz gerekmektedir.
Bir diğer nokta da üretim değişkenliklerine bağlı olarak zamana yayılan tüketim anomalilerini tespit etmektir. Ani oluşan bir üretim talebinin hatlarınıza yansıtacağı tüketim değerlerini tespit edebilirseniz, bu projelerin sizin gerçek karlılığınıza etkisini de bileşenlerine dağıtabilirsiniz. Bu tür bir tespit için de yine enerji tüketimi verilerinizi bileşenler bazında görüntüleyebilmek için verileri toplamak, kaydetmek ve analitik amaçla kullanmak gerekmektedir.
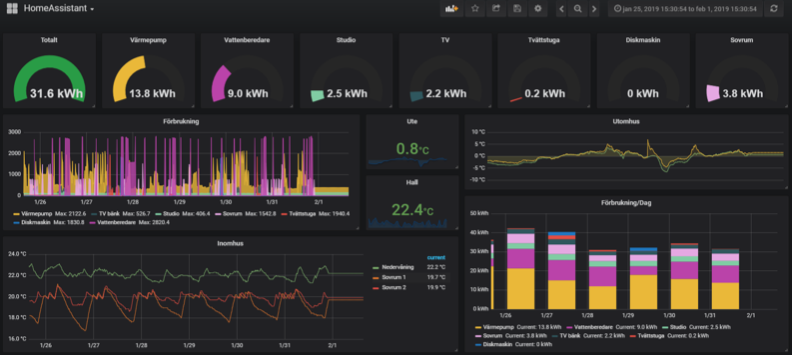
HVAC (Isıtma, Soğutma ve Havalandırma) sistemleri de fabrikaların enerji tüketim değerlerini önemli ölçüde etkileyebilmektedir. Bu tür sistemlerin de toplam maliyetlere etkisinin dağıtılabilmesi için yine buradaki tüketim toplamlarının bileşenler bazında alınması bir enerji yönetimi yaklaşımı olarak karşımıza çıkmaktadır.
Özetlersek, Fabrikanız için yapacağınız bir enerji takip izleme sistemi, size yatırım kararlarınızda, verimlilik artışınızda ve dolayısıyla da tasarruflarınızda yön verecektir. Fabrikanızın tüketim trendlerini takip etmenize, hat ve ürün üretim maliyetlerini belirlemenizde yardımcı olacaktır. Olağandışı tüketimler için üretilecek alarmlarla sizi kayıplardan ve kaçaklardan koruyacak, cihazlarınızın ömrünü artıracak ve plansız kesinti risklerinden uzak tutacaktır.